DAWSON Engineering Team
At DAWSON we specialize in design for manufacturability, helping our customers save cost and receive product on time
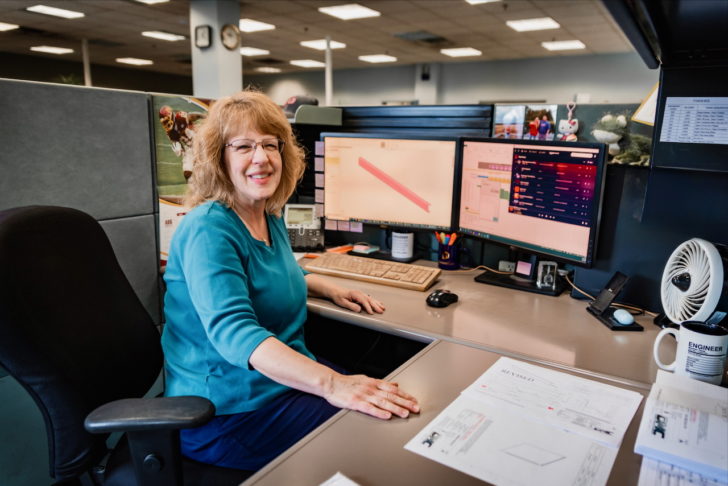
DAWSON’s highly skilled workforce use one-of-four of the latest, and trusted, welding techniques in our manufacturing process.
DAWSON has numerous spot welding machines suitable for welding various materials.
Our newest spot welding machine is the Amada ID40IV HP NT. The ID40IV HP NT features the latest inverter spot welding technology that is capable of consistently producing high-quality sparkless welding.
Vertical press type welding combines the power of inverter technology with the accuracy of a microcomputer controller. The integrated AMNC PC touchscreen control provides storage and editing capabilities of welding programs and conditions.
Many of our welders are AWS (American Welding Society) certified. Being AWS certified indicates that the welder has completed a welder performance qualification test. DAWSON uses an AWS CWI (Certified Welding Inspector) to produce documentation, welding procedures and to qualify welders.
All welders (when applicable) follow AWS standards D1.3/D1.1, D9.1, D15.1, D1.6, D2.2.
A quick, semi-automated arc welding technique, joins two base materials together. The mechanism involves a continuous solid wire electrode, being fed through a welding gun and into the weld pool. Simultaneously, a shielding gas is also sent through the welding gun, protecting the weld pool from contamination.
For use on aluminum, steel galvannealed, and stainless steel materials ranging from .020” to 1”.
Requiring a higher skill level, this manual arc welding process uses the heat of an electric arc between a tungsten electrode and the base metal; a unique mechanism that sets this method apart from the rest. A separate welding filler rod is fed the molten base metal if needed, and a shielding gas flows around the arc to keep air away, and other impurities.
For use on aluminum, steel, galvannealed Muntz, commercial bronze, and stainless steel materials ranging from .020” to 1”. A silicon bronze tig rod is used when applicable.
A fully automated technology, this welding technique involves an ARC Msate 120iB robot within DAWSON’s Robotic Weld Cell. This technique requires our skilled welders to load, and unload fixtures and inspect product through to completion. The Weld Cell is set up with two weld tables containing a series of holes that allow for modular fixturing.
For use on steel and stainless steel materials.
Efficient, safe, clean, and environmentally conscious, this welding technique is a reliable mechanism for the formation of an electro-mechanical joint. DAWSON’s facilities house many spot welding machines suitable for welding various materials.
For use on steel, stainless steel, aluminum, and brass materials.
With outstanding versatility, this process makes a great choice for rusty or unclean surfaces. Stronger than MIG welding, stick welding tends to penetrate more further. This type of welding is also known as manual metal arc welding (MMA or MMAW), shielded metal arc welding (SMAW), and flux shielded arc welding.
For use on steel, and stainless steel materials ranging from .125” to 1”.
Used commonly for dissimilar metals, a process of joining two or more metal materials together by melting and flowing a filler metal into a joint, with the filler metal having a lower melting point than the joined materials.
For use on all types of materials and applications.
A term to describe any welding process that uses heat to combine (or fuse) two or more materials into a melting point by heating them. This process may or may not involve a filler.
For use on all types of materials and applications.
At DAWSON we specialize in design for manufacturability, helping our customers save cost and receive product on time
DAWSON’s facilities house multiple state-of-the-art lasers, with full sheet stock cutting capabilities.
Complex sheet metal component shapes are achieved through precise, programmed machinery.
Our equipment utilizes a superior and more efficient air bending technique for seamless pieces.
DAWSON operates leanly with work stations and equipment arranged to accommodate a one piece flow, for efficient manufacturing and quality assurance.
Reviews, inspections, and tests are regularly conducted at appropriate stages to verify that the requirements have been met.
A full range of mechanical fastening options are available to achieve your project’s requirements.
Our in-house, high-performance machine tool, meets the precise requirements needed to produce the high quality parts you demand.